Air Compressor - Powerful and Efficient Solutions for Your Needs
Introduction:
An air compressor is a pneumatic device that can power a variety of tools. Air compressors work by putting atmospheric air under high pressure, “compressing” the air and converting its potential energy into kinetic energy that it stores in an air tank for use.
Type of air compressor:
- Reciprocating Air Compressors
- Rotary Screw Air Compressors
- Axial Compressor
- Centrifugal Compressor
Air compressor Used
Some of the most common uses of air compressors are in everyday items like refrigerators, air conditioners, and vehicle engines. In construction, they’re used in a variety of different tasks and settings, like inflating tires and powering HVAC systems, air tools, and industrial systems.
So, how does an air compressor get air? For those that use pistons, it involves two parts: Raising the pressure and reducing the volume of the air. Most compressors use reciprocating piston technology.
An air compressor typically uses:
- An electric or gas motor
- An inlet and a discharge valve to draw in and release air
- A pump to compress the air
- A storage tank
The compressor draws in air and creates a vacuum to reduce its volume. The vacuum pushes the air out of the chamber and into its storage tank. Once the storage tank reaches its maximum air pressure, the compressor turns off. This process is called the duty cycle. The compressor will turn back on when the pressure drops below a specific number.
A regulator attaches to the outlet for your compressor’s air tank and features an adjustable nob and a pressure indicator. As you rotate the knob counterclockwise, it pushes on a spring which restricts a valve, which lowers the pressure by reducing the supply of air entering the regulator. When you turn the knob clockwise, the spring and the valve release, allowing more high-pressure air through the output.
For many single-stage air compressors, this limit is reached, a pressure switch goes off to stop the motor and the production of compressed air. In most operations, you don’t need to reach that pressure limit, so many compressors set air lines to a regulator. With a regulator, you can input the appropriate pressure level for a given tool.
When the amount of pressure needed to power your tool is lower than the pressure in your air pressure tank, a regulator adjusts the pressure for you. While the regulator can’t raise the pressure above what’s already in your tank, it ensures your tool gets a consistent flow of air at the correct pressure.
When the specified pressure is reached, the regulator shuts off the pump at any point in its cycle, which means the piston can be halfway through a stroke, with pressurized air in the chamber, when it stops. This air can put undue pressure on the starting circuit, which needs more power to start the motor. An unloader valve is a simple addition that releases the trapped air to avoid this problem.
A regulator is bookended by two gauges — one to monitor the pressure of the tank and another to monitor the pressure within the air line. Also, the tank has an emergency valve that triggers if the pressure switch malfunctions.
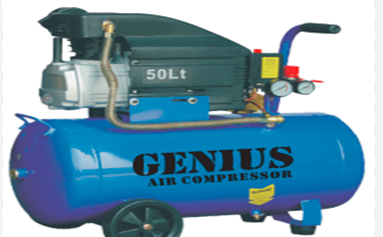
Compressed Air in Everyday life
From pneumatic drills and braking systems to HVAC units, a wide range of air-powered tools and machines make everyday life convenient, safe, and efficient. In nearly every building you walk through or pass by on a given day, air tools helped someone sand the wood, paint the walls and hammer beams and plasterboards into place. On shop floors across the world, people use compressed air to add coats of paint and blast dust and debris away.
It’s nothing short of remarkable that humankind discovered a way to take ambient air, perhaps the most abundant resource on the planet, and transform it to power motorized equipment for a wide variety of purposes.